Featured Products:
Product Description
How It Works
DEACTIVATOR chemically reacts with the alkalies in concrete
to instantly prevent fresh concrete from bonding and to
gradually soften existing concrete buildup. Applied daily before
use, DEACTIVATOR prevents adhesion and accumulation of
concrete buildup on treated surfaces.
Applications
Use in all block, pipe, ready-mix and cement plants for
treating mixers, cement hoppers, conveyors, elevators,
chutes, pallets, pipe rings and hoist buckets.
Use on bridge and street paving machines, laser screeds,
vibratory roller screeds, truss screeds, median barrier and
curb slipform machines, strike-off augers, hoppers and
slipforms.
Use on shoring, scaffolding and forming equipment and
hardware, including post shores, scaffold frames and planks,
aluminum deck beams and joists, column clamps, waler rods
and shebolts.
Advantages
Chemically softens concrete buildup and prevents
adhesion and buildup on treated surfaces.
Makes chipping hammers and chisels obsolete.
Will not harm rubber hoses or damage painted metal
surfaces.
Concentrated petroleum based formulation can be either
diluted or used full strength.
DEACTIVATOR is petroleum based. DEACTIVATOR E
is water based. DEACTIVATOR E is also available in
a concentrated version which is shipped in short-filled
containers.
Will not wash off in rain.
DEACTIVATOR E is Green Engineered™ – better for
health and the environment.
Non-flammable.
Guaranteed! Money back guarantee if not fully satisfied
with the results.
DEACTIVATOR E complies with the more restrictive air
quality, lower VOC requirements of some states.
Manufacturer Info
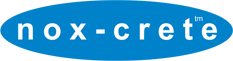
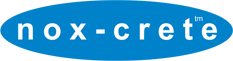
Nox-Crete™
In 1956, Carl Linn introduced the world’s first chemically active form release agent.
While working as a chemist for the United Petroleum Group in Omaha, Nebraska, Linn noticed concrete contractors were using the company’s oil and grease compounds to prevent fresh concrete from bonding to forms. Not only were the oil and grease compounds difficult to work with, but the resulting concrete was discolored and unpaintable. Plywood forms also suffered, failing after just a few pours. Concrete workers had struggled with these issues for years, but Linn had an idea.
He developed a chemically active release agent, Nox-Crete Form Coating, and a chemically active form maintenance product, Nox-Crete Deactivator. With Nox-Crete Form Coating, contractors produced concrete that looked better and wood forms that lasted longer. With Deactivator, the concrete buildup could be safely and easily removed from tools and equipment.
Today, Nox-Crete continues to manufacture chemical solutions to concrete problems.