Featured Products:
Product Description
Simple:
Easy to use with fewer parts and pieces than most handset systems, and requires less lumber and nailing.
Versatile:
Perfect for a wide variety of heights, shapes, and radii, as well as specialty job-site considerations.
Quality Finish:
Achieve an architectural finish with an easily adaptable, customizable handset system.
Cam-Lock Bracket:
Easy to use clamp and bracket assembly engage the loop end tie, securely holding the 2×4 waler in place.
Ties:
All ties are manufactured in Denver, Colorado in standard 1”, 1.5”, and 2” break back depths, and can be custom made to suit various applications.
Scaffolding:
Our integral OSHA compliant scaffolding system attaches to the back of the CamLock Bracket.
Manufacturer Info
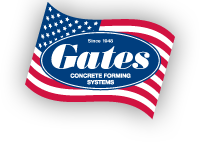
Gates®
Gates & Sons’ History goes back to the late 1920s, when Lee Gates, Sr. invented his first twisted-wire form tie with a built-in spreader.
Until that time, most forms for concrete wall foundations were built with 1 x 8″ sheating boards, vertical 2 x 4 studs on 24″ centers and held together with No. 9 black annealed soft wire to receive the wet concrete. 100lb coils of wire were delivered to the job site along with the 1 x 8″ and 2 x 4 lumber. The No. 9 wire was job-cut to the proper length, bent ‘U’ shape to go around the two opposite vertical 2 x 4 studs, and placed between every other joint of the 1 x 8″ sheating boards. As boards were added, the two strands of wire were center-twisted with a large screwdriver, or pin, against a 1 x 2″ wood spreader cut to the desired wall thickness …one tie at a time…a very slow process!
While working on a new all-concrete mausoleum at Crown Hill Cemetery in northwest Denver, Lee Gates conceived the idea that a pre-twisted form tie could speed up the formwork. In the early development of his idea, he found that by using 5/8’s smooth carbon-steel rods to replace the vertical 2 x 4’s, additional speed in building the form was possible with his new tie. He started at once to design and build machines to manufacture his new ‘twisted-wire’ form tie. His new tie gained wide acceptance in and around Denver and the Colorado area.
Following World War II, 3/4″ form plywood became readily available at an affordable price. Lee Gates’ 4-strand, center-twisted tie made from black wire (that rusted) was then re-designed into a stronger, 3-strand, 11 gauge galvanized tie (no rust) and twisted from one end on automatic machines. Tie slots were routed in 2′-0″ x 8′-0′ plywood panels and the 5/8″ carbon-steel rods were run horizontally, creating a very fast, lightweight, inexpensive forming system!
To meet the greatly expanding home-building market that followed World War II, a national sales program was put into place. Later, other Gates forming systems were developed and patented for the commercial construction trade, making Gates & Sons a leader, nationwide, in forming systems today!
Lee Gates, Sr. lived to see his twisted-wire tie invention transform concrete construction. He died on April 7, 1975, at the age of eighty-one and is buried just a few hundred feet south of the mausoleum where his first form ties were used.